The Plan-Do-Check-Act cycle is a model/technique in the Quality Management System used for carrying out change. It is a simple four-stage method that enables teams to avoid recurring mistakes and improve processes. It can be used to plan new projects that aim to deliver new products or services. It is a key prerequisite for the continuous improvement of people and processes.
Table of Contents
Walter Shewhart first proposed PDCA later developed by William Deming. At first, he developed a 3-step repeating cycle for process improvement, also known as “the Shewhart cycle”. The three phases of this cycle were:
- Specify
- Produce
- Inspect
Years later, inspired by Shewhart’s ideas, William Deming expanded the model into a learning and improvement cycle and developed an iterative process of continual improvement known as the PDCA cycle.
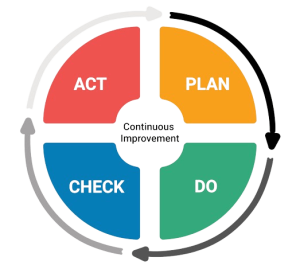
Because one of MVS Pharma’s main goals is to be transparent in all its endeavors, we have created a Quality Management page where you can explore our QM methods briefly. Let’s discover each stage of the PDCA cycle and the benefits it will bring to your processes.
Step 1. PLAN – Quality Management System
PLAN stage of the PDCA cycle: At this stage, you will plan what needs to be done. Depending on the project’s size, planning can take a major part of your team’s efforts.
- Objective: Identifying a problem or area that can be improved and addressed.
- Activities: Data collecting; setting goals, analysis of the current process, and developing a detailed plan to take action.
- Focus: Designing and deciding the desired outcome, also establishing measurable objectives and criteria that can lead to success.
Before you move to the next stage, you need to be sure that you answered some basic concerns:
- What is the core problem we need to solve?
- What resources do we need?
- What resources do we have?
- What is the best solution for fixing the problem with the available resources?
- In what conditions will the plan be considered successful? What are the goals?
Step 2. DO
DO Stage of PDCA cycle
After you have agreed on the plan, it is time to take action. At this stage, you will apply everything that has been considered during the previous stage.
- Objective: To implement the action plan on a small scale, sometimes it can sometimes be a test or pilot.
- Activities: Fulfilling the plan while collecting enough data for monitoring the progress.
- Focus: Here is important for the team to ensure that the execution follows a designed plan; any changes or issues made during the implementation must be documented.
Step 3 of Quality Management System technique: CHECK
CHECK stage of the PDCA cycle
This is probably the most important stage of the PDCA cycle. If you want to clarify your plan, avoid recurring mistakes, and apply continuous improvement successfully, you need to pay enough attention to the CHECK phase.
- Objective: Expected outcomes are compared to the results of the implementation. This is done so the results can be evaluated.
- Activities: To analyze all the data collected while executing the “Do” phase to determine if the set goals are met.
- Focus: To identify failures, successes, and what can be improved further. This is the time to audit your plan’s execution, and if something goes wrong during the process, find the root cause of the problem.
Step 4. ACT
ACT stage of the PDCA cycle
Finally, you arrive at the last stage of the Plan-Do-Check-Act cycle. Previously, you developed, applied, and checked your plan. Now, you need to act.
- Objective: Using the evaluation results, actions for implementing improvements permanently are taken, or adjusting the plan as needed.
- Activities: In case the outcome is successful, standardize the solution and completely implement it. If something is not working correctly or expected results are not being achieved, then necessary adjustments have to be made and go through another repeat of the cycle.
- Focus: Insert successful practices into the organization’s standard processes and ensure continuous monitoring for improvement.
In conclusion, if you apply effectively all four stages, your PDCA model will become the new standard baseline. However, every time you repeat a standardized plan, remind your team to go through all the steps again and try to improve carefully.
Disclaimer
As a service to our readers, MVS Pharma GmbH publishing provides access to our archived content library in our blog. Please note the date of the last review or update on all articles. No content on this site should ever be used as a substitute for direct medical advice from your doctor or other qualified clinician.
MVS Pharma GmbH will soon be launching the MVS Omega-3 medical-grade dietary supplement onto the European market, which has been developed for the highest quality standards in terms of oxidation avoidance and therefore greatest bioavailability. In addition, in vitro studies are currently underway at the University of Ulm, in which Professor Dr. Rüdiger Groß tested a patented mouth and nose spray (Virudol) that can eliminate various flu viruses based on natural substances.
In addition, MVS has a wholesale license and has specialized in sourcing much-needed medicines such as Amoxicillin, Salbutamol, etc. from India through its local branch with a focus on local quality and safety testing, compliance with international GMP regulations and the highest quality level of user security (examples of local language brochures, identical units of measurement, batch control and full tracking, etc.).